صنایع نساجی شامل همه مراحل تولید انواع الیاف، تبدیل الیاف به نخ، تبدیل نخ به انواع پارچه و همچنین شامل فرایندهای تکمیل بر روی پارچه و منسوجات مانند رنگرزی و چاپ است. صنعت نساجی تمام حوزههای مربوط به پوشاک و منسوجات را شامل میشود و کسانی که میخواهند در این بخشها کار کنند باید به مراحل تولید و ماشین آلات نساجی آشنایی داشته باشند.
سیستم ریسندگی فیلامنت
معمولاً، فیلامنت در سیستم ریسندگی ذوبریسی بهوسیلهی تبدیل پلیمرها به چیپس (Chips)، رنگرزی ذوب و الکترود نمودن در مرحلهی پلیمریزاسیون انجام میگیرد. امروزه، تحقیق و توسعهی صنعتی روش پلیمریزاسیون مداوم مستقیم را بهعنوان یک متد تکنولوژیکی برای کاهش مصرف انرژی عمومی شناخته است. در این روش پلیمر مذاب بهصورت مستقیم به ماشین ریسندگی تغذیه شده و از مرحله پلیمریزاسیون بدون تبدیل شدن به چیپس میگذرد. افزایش سرعت ریسندگی به تنهایی برای بهبود راندمان تولید خیلی ایدهآل است اگر بتوانیم افزایش سرعت رو به ازدیادی در مرحلهی ریسندگی الیاف کوتاه داشته باشیم.
فیلامنت پلیاستر عموماً توسط سرعتِ ریسندگی ۱۰۰۰ تا ۱۵۰۰ متر در دقیقه، برداشت یکباره و کشش چهارمرحلهای یا پنجمرحله بزرگتر تا رسیدن به تنش قابلقبول صورت میپذیرد. در ماشین برداشت در سرعت ۳۰۰۰ تا ۴۰۰۰ متر در دقیقه، سرعت ریسندگی افزایش یافته، مولکولها بهصورت نسبی آرایش یافته و نخِ نسبتاً یکنواختی تولید که بهنام Poy شناخته میشود. در مرحلهی تاب مجازی، کشش مورد نیاز راتأمین مینماید. بهعلاوه ماشینهای برداشت در سالهای اخیر تا سرعت ۶۰۰۰ متر در دقیقه افزایش یافتهاند و بههمین دلیل آرایش یافتگی مولکولی در این سرعت بسیار بهتر صورت پذیرفته و نخِ تولیدی به آرامی کشش یافته و برای انتقال به مراحلِ بعدی ریسندگی آماده میگردد.
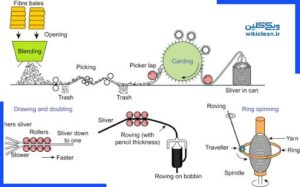
این آرایشیافتگی بالا یا Hoy حد آمادگی برای کشیدگی در قیاس با کشش مورد قبول نخ است. در نتیجه راههای مختلفی برای روش Hoy برای تولید نخ کششیافته در قسمت کشش بهوسیلهی حرارت یا سرد نمودن و … وجود دارد. هر دو عامل سرعت بالایِ ماشینِ برداشت، اتوماسیون و بزرگ شدن بستههای تولیدی در پیشرفت بیشتر برای کاهش ضایعات، افزایش راندمانِ تولید بههمراه عملیات ریسندگی با سرعتِ بالا و تعویض اتوماتیک در ماشینِ برداشت، از جمله مواردی است که مخصوصاً در آمادهسازی برای کار بدون حضور اپراتور در کارخانجاتِ نساجی انجام شده است. برداشت فیلامنتهای چندلا در یک پوزیشن، بین ریسندگی و مرحلهی برداشت برای تولید بیشتر نخهای فیلامنتی در یک فضای باریک با مصرف کمِ انرژی مؤثر بوده و بهمنظور افزایش تولید، مناسب است. مطابقِ روال، یک یا دو اسپیندل ریسندگی غالباً مشترک بوده اما در فیلامنتهای ظریف برای چهار تا هشت اسپیندل، برداشت با همان شرایطِ قبلی است.
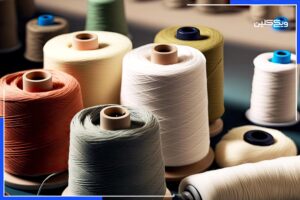
درحال حاضر با پیشرفت تکنولوژی در قسمت Poy سرعت تابندگی برای کشش و تاب افزایش یافته و ماشینها معمولاً در زمان تولید پلیاستر با ۸۰۰ متر در دقیقه و در زمان تولید نایلون با ۱۰۰۰ متر در دقیقه کار مینمایند. اگر قسمت به قسمت در نظر بگیریم واحد حساسِ تابِ مجازی در طی مطالعات تحقیقاتی انجام گرفته جهت عملکرد بالا با دیسکهای اصطکاکی و سیستم تسمههای فشرده به صورت صنعتی مجهز شدهاند. در ماشینهای تکسچرایزینگ تغییرات قابلتوجهی صورت گرفته است. این تغییرات تجهیزاتی شامل استفاده از هوا برای عمل تکسچرایزینگ و در نتیجه انواع مختلف نخهای مشابه نخهای ریسندگی از فیلامنتها تولید میگردد.
مراحل تولید الیاف استیپل (کوتاه، بریده شده)
در مرحلهی ریسندگی، روش پلیمریزاسیون مداوم مستقیم، به یک روش اصلی تبدیل گردیده است. این روش تولیدِ نخ توسط تغذیهی پلیمرِ مذاب مستقیماً از مرحلهی پلیمریزاسیون به ماشین ریسندگی صورت میگیرد. بههرحال در تولید الیاف چندجزئی در مقیاسِ کوچک چندجزئی، مرحلهی تبدیل بهبود یافته است. آنچه مرسوم است پلیمر بهصورت چیپس (Chips) در مرحله پلیمریزاسیون و پس از خشک نمودن چیپس، آنرا ذوب نموده و با عملِ الکترود نمودن به فیلامنت تبدیل میشود. در این مرحله افزایشِ سرعتِ ریسندگی، به بهبود و افزایشِ راندمان کمک مینماید، چراکه اسپینرت دارای تعداد زیادی سوراخ با ظرفیتِ بالاو گسترده هستند.
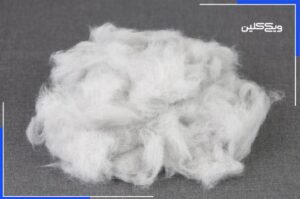
اسپینرت تقریباً ۲۰۰۰ سوراخ و در قیاس با تغییرات مورد تولید که افزایش در حدود ۱۰۰۰ سوراخ در هر بار است. بعضی از اسپینرتها جهت کاهش هزینهی مطمئن بین ۳۰۰۰ تا ۴۰۰۰ سوراخ دارند. امروزه با افزایش ظرفیت ریسندگی، کنهایی با ظرفیت نگهداریِ ۱۰۰ تا ۳۰۰ کیلو و رنجِ ۱۰۰۰ تا ۳۰۰۰ کیلو جهتِ نگهداری فیلامنتهای ریسیده شده ساخته شده است. همزمان نقل و انتقال کنهای بزرگ مشکل بوده و بههمین دلیل از لیفتراکهای برقی یا تسمه نقاله استفاده میشود. در این ارتباط از خطوط ترانسپورت تسمهنقالهای فول اتوماتیک به جهت کاهش نیروی انسانی و اطمینان از هزینهی تولید با مرتبط نمودن خطِ تولید با قسمت تغذیهکنها استفاده میشود.
رشد روزافزون تکنولوژی در مراحل کشش کمک شایانی برای تولید با ظرفیت بسیار بالا با سرعتهای زیاد نموده است. افزایش ظرفیت در رنجهای ۲۰۰۰ تن و ۳۰۰۰ تن در روز از ظرفیتهای قبلی ۵۰۰ تن و ۱۰۰۰ تن در روز و سرعت افزایش سرعت در قسمت کشش ۲۰۰ تا ۳۰۰ متر در دقیقه در بر داشته است. درحالیکه در گذشته نهایت سرعتها بین ۱۰۰ تا ۱۵۰ متر در دقیقه بوده است. بهطوریکه مدلِ جدید ماشینهای خیلی بزرگ با ظرفیت ۵۰۰۰ تن در در روز با سرعتِ ۳۰۰ متر در دقیقه ساخته شده است.
بهمنظورکاهشِ قیمت، ظرفیت بالا و سرعت بالا بههمراه کنترل دقیقِ مراحل، تعداد قابل توجهی تحقیقات انجام گرفته که هم در کاهش قیمتِ تمامشده و هم در افزایش ظرفیت بسیار مؤثر بوده است. این سیستم بهنام Spin-Draw و سیستم عملیاتی مستقیم معروف شده است. اما کلید موفقیت سیستم در این حقیقت که افزایش سرعت برای هر قسمت و درنتیجه توسعه عملکرد تولیدات با این روش، نهفته است. موفقیت باارزش دیگر در طراحی اجزاء حساس و مهم قسمت کریمپر و افزایش سرعت ادوات کاربردی برای مشابهسازی فروموج طبیعیِ نخهای ترکیبی غیرفلزی است.
ماشین های ریسندگی
توسعه و رشد تکنیکی و اتوماسیون در ژاپن در همین سالهای نزدیک شروع شده است. امروزه بیش از ۳۵۰،۰۰۰ اسپیندل بهصورت مداوم و اتوماسیون در مرحلهی مخلوط نمودن، حلاجی و کاردینگ تا مرحلهی کشش که براساس آخرین تغییرات و بهروز شدن، در ژاپن کار میکند. سیستم شوتفید براساس نیاز ۳۵۰،۰۰۰ اسپیندل برای مراحل مداوم مخلوط نمودن، حلاجی تا کاردینگ که کاملاً مؤثر بوده و در جهت اتوماسیون و کاهش هزینهها نقش دارد طراحی شده است.
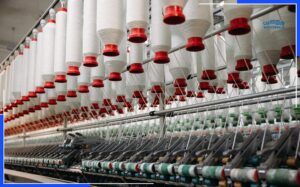
بههرحال این سیستم در انواع مختلف مناسب برای کنترل میزان تغذیه و قابل تنظیم برای هر میزان تغییر در تغذیهی مواد ساخته شده است. در نتیجه برای پارتهای مختلف تولید، داف اتوماتیک و ادوات و تجهیزات نقل و انتقال در سیستم بالشچه آماده و اجرائی شده است. بالشچه و فتیله در خیلی از مواقع خارج از محل اصلی و در انواع مختلف بهصورت اتوماتیک تغذیه شده و رشد تکنیکی زیادی را برای مراحل اتوماسیون میطلبد. در بخش کاردینگ، افزایش سرعتها، تولید به ۱۰۰ کیلوگرم در ساعت با تغییرات مطمئن در اصول کاردینگ و بهبود عملکرد در قسمتهای بازکنندهی الیاف، رسانده است.
البته غلتکهای داخلی وجود سیستم جفت کویلر و اتوماسیون عملکردهای جنبی مثل: سیستم جمعآوری ضایعات و گردوغباردر این افزایش تولید مؤثر بوده است. افزایش سرعت و یکنواختی تولید در ریسندگی در بخش شانه، سیلندر سوزنها، با بهبود صفحات خاردار با سیلندر خارهای سیمی و یا هر دو صفحات استیل سوزنی، امکانپذیر گشته است. در حال حاضر عملکرد شانه تقریباً به ۲۴۰ تا ۲۵۰ نیپ در دقیقه رسیده است. بالشچه به صورت اتومات تغذیه و عملکرد اتوماتیک دافر نیز به این افزایش سر عت کمک نموده است. در قسمت کشش، سرعت تولید با بهبود مکانیزم کشش به ۵۰۰ متر در دقیقه رسیده است. در مرحلهی نیمچه نخ، پیشرفت بزرگی با ساخت ماشینهای سرعت بالا و بستههای تولیدی حجیم و توان تولیدی ۱۲۰۰ تا ۱۴۰۰ دور در دقیقه برای فلایر و برداشت ۱۴ تا ۱۶ اینچ، صورت پذیرفته است. حاصل همهی این موارد، سهولت سیستم داف که قادر است بدون برداشتن فلایر کار نماید، اتوماتیک بودن دافر، کمک شایانی به بهبود عملکرد ماشین نیم-تاب یا فلایر نموده است.
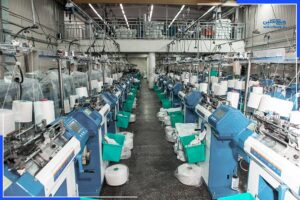
در مرحلهی ریسندگی، عملکرد کاملاً یکنواخت بهوسیلهی غلتکهای دقیق و دقت عمل اسپیندل، کار ریسندگی را به بهترین شکل ممکن میسازد. در ژاپن تقریباً نیمی از دوکهای ریسندگی مجهز به داف اتوماتیک برای کاهش هزینهها گردیده است. اتوماسیون مقدمات تولید و بعد از تولید فتیله، نیمچه نخ و نخ و … در شرایط تولید و جابهجایی مواد اولیه اهمیت زیادی برای ماشینهای ریسندگی دارد. دافر اتوماتیک و گرهزن اتوماتیک نخ در ماشینهای ریسندگی مثال خوبی برای استفادهی درست از تکنولوژی است.
موارد مطرحشده در تعدادی از ماشینهای ریسندگی در ژاپن است که یک سری از گرهزن نخ در مراحل پیوستهی کار و موارد غیر پیوسته در قفسههای ریسندگی، برداشت نخِ نیمتاب تا مرحلهی پیچش نخ ریسیده شده روی بوبین بهصورت اتوماتیک شده است که اتوماسیون گرهزنِ نخ با یکدیگر یعنی اتوماسیون دافر هماهنگ گردیده است. در ماشینهای سیستم ریسندگی اُپن-اند از نوع روتور سرعتها تا ۸۰۰۰۰ دور در دقیقه افزایشیافته است.
این ماشینها برای داف اتوماتیک آسان و تولید بستههای حجیم نخِ تولیدی طراحیشده است. گستردگی قابلتوجه در کاهش هزینه مخصوصاً در مرحلهی ریسندگیِ نخهای مغزی ایجادشده است. در ژاپن ۲۵۰۰۰۰ چشمهی ریسندگی اُپن-اند در حال فعالیت بوده و تغذیهی اتوماتیک باسرعت بالا با درام تمیزکنندهی داخلی و غیره. با گسترش و بهبود عملکرد ماشینها درمجموع به جهت گسترش نخهای قابل ریسیدن و بهبود کیفیت نخ، از نکات مثبت این پیشرفت است. در ماشینهای ریسندگی اُپن-اند برای الیاف بلند نیز پیشرفت قابلملاحظهای وجود دارد. معمولاً سیستم ریسندگی اُپن-اند با سیستم روتور شناخته میشود، اما مدلهای دیگر سیستم ریسندگی اُپن-اند مثل ایروُرتکس که بنام ماشینهای سیستم ریسندگی پیچشی شناخته میشود نیز تولید میگردد. این ماشینها هم عملاً در حال کار هستند و هم نمرات ظریف با سرعتِ ۱۴۰ تا ۲۰۰ متر در دقیقه تولید میکنند. بهصورتیکه رسیدن به یک تحول بزرگ و کامل را در ماشینهای ریسندگی امکانپذیر ساختهاند.
سیستم ریسندگی فاستونی
اسم دیگر آن سیستم ریسندگی الیاف بلند است. سیستمهای شستشوی پیشرفته همچون سیستمهای شستشوی قلیائی، سیستم جت و برای شستشوی پشم وجود دارد. اما این سیستمها غالباً برای جداسازی شن و سنگهای ریز موجود در پشم کاربردی ندارند. اصولاً برای شستشوی پشم از ماشینهای شستشویی استفاده میشود که مخازن شستشوی آن عمق زیادی داشته باشد.
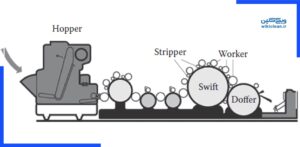
جهتِ تولید محصولات نساجی با مواد اولیهی مختلف، انواع ماشینها با راندمانِ بالا همچون بازکنندهی الیاف تغذیهکننده با مقدار دقیق تغذیه، میکسر مناسب و با راندمان و کیفیت خوب ، تغذیهکننده پشم اتوماتیک و … مراحل تولید مداوم مطابق با استانداردها و شرایط مطلوبِ تولید، با ترکیبِ نسبتاً خوب این ماشینها امکانپذیر است. انواع کاردینگهای غلتکی سیلندری متناسب با انواع مواد ریسندگی، مطابق با نیاز کیفی و میزان ریسندگی موردنیاز، توسط سیلندر کاردینگ با عرضِ ۱۵۵۰ تا ۳۰۰۰ میلیمتری ساخته شدهاند.
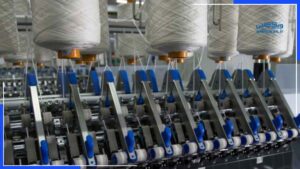
بهبود کیفیت سرعتبالا و تولید بالا بهوسیلهی اختراع نوارهای متالیک، افزایش کیفیت مواد و مراحل تولید دقیق با جفت دافرها بهدستآمده است. تولید بالا با اطمینان از عملکرد شانه که کیفیت و توان تولیدی فتیله با ۱۶۰ نیپ در دقیقه را دارد حاصل میگردد. در حال حاضر سرعت ۱۸۵ نیپ در دقیقه برای ماکزیمم نرخِ تغذیهی ۴۵۰ گرم در متر در نظر گرفته شده است. در سالهای اخیر سیستم تغذیهی مواد برای شانه بر اساس تغذیهی بالشچه که رشد و توسعهی این ماشینها موجب تولید بستههای بزرگ بالشچه که به-منظور کاهش هزینه درکل، طراحی شدهاند، امکانِ پیچش بستههای تا ۱۷۰ کیلوگرمی را داده است. مدلِ عمومی این ماشین، ماشین گیل، مخلوطکن و مرحلهی کشش با گیلِ میانی که موتور آن مجهز به اسکرواست. این ماشین با سرعتِ مطمئن ۲۲۰۰ دراپ در دقیقه کار میکند.
منبع: مجله «کهن» (مجله اختصاصی صنعت نساجی و فرش ماشینی ایران)
لینک کوتاه: https://wikiclean.ir/v9jn